- 针对虫情进行自动监测、预警,并结合生产车间治理情况提供辅助决策功能。
- 针对车间环境空气质量(重点为TVOC)进行自动监测,车间化学防治后提供药剂残留检测,确保人员安全。
- 在生产车间高架库等区域安装高空自动巡检装置,对高空虫情及环境空气质量进行巡检,避免监测盲区。
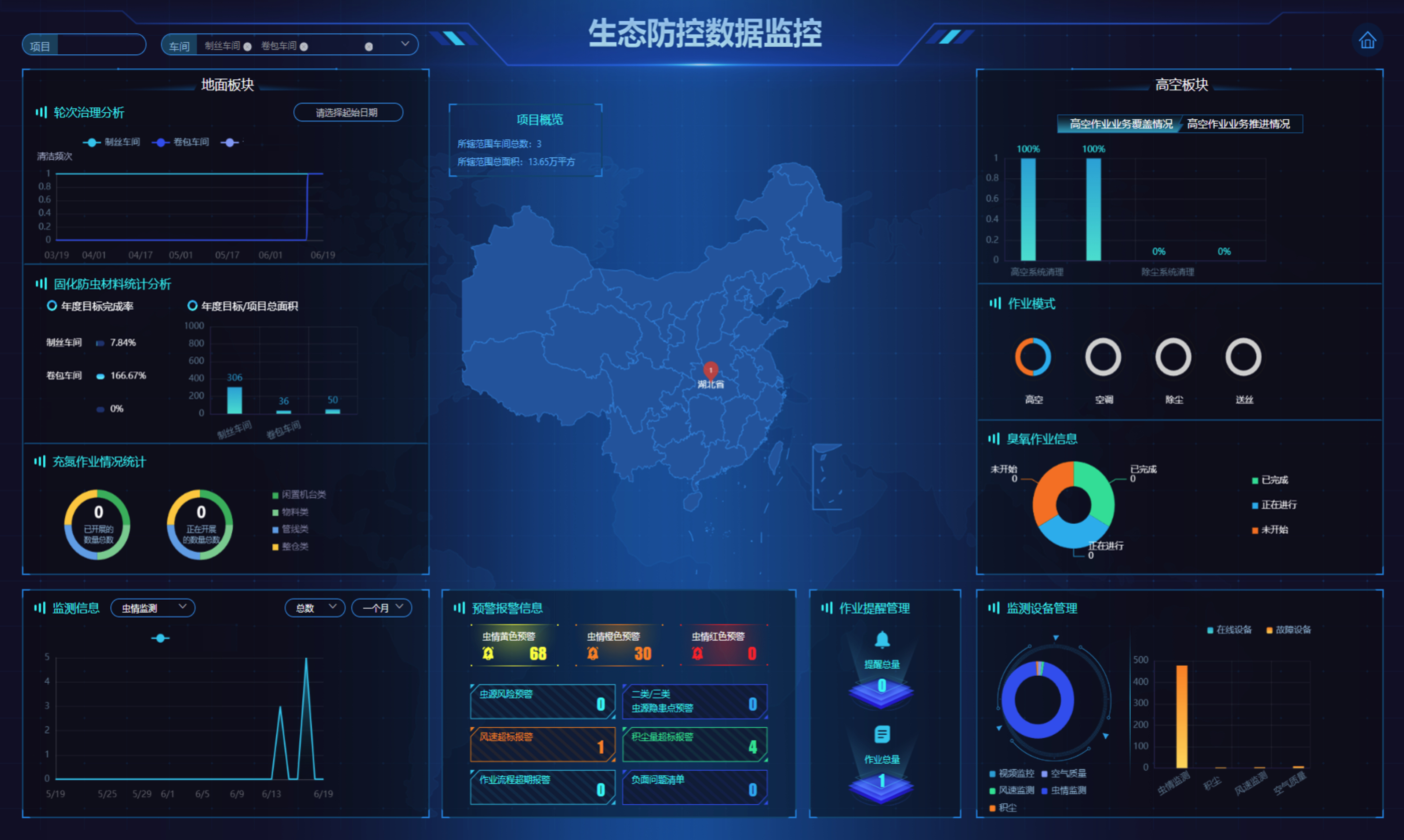
- 虫源隐患深度清除:以建立涵盖生产车间、高空、管线的全面虫源隐患清单,定期开展虫源隐患深度清除工作。
- 固化防虫材料布放与回收:针对不易清洁且虫源反复滋生点位(电控柜、线槽等),布放固化防虫材料实现长效防虫(食物引诱剂诱捕、生物杀虫剂杀虫)。
- 定点滞留喷洒:针对不易清洁的虫情滋生点,采用安全、高效的药剂,进行定点药剂防治,避免虫情反复滋生。

- 闲置设备、管道等混合气调快速杀虫:针对闲置设备、管道等,采用二氧化碳留滞型“双工制氮”设备进行充氮+二氧化碳混合气调快速杀虫技术,缩短充氮杀虫时长。
- 暂存物料保湿充氮防虫:针对染虫及暂存物料,采用常压运行保湿制氮技术应急杀虫,避免物料水分流失造成品质劣变。
- 车间独立分区整仓充氮杀虫:针对生产车间独立分区,可采取整仓充氮进行全局治理,对区域内所有虫源点达到有效杀灭。
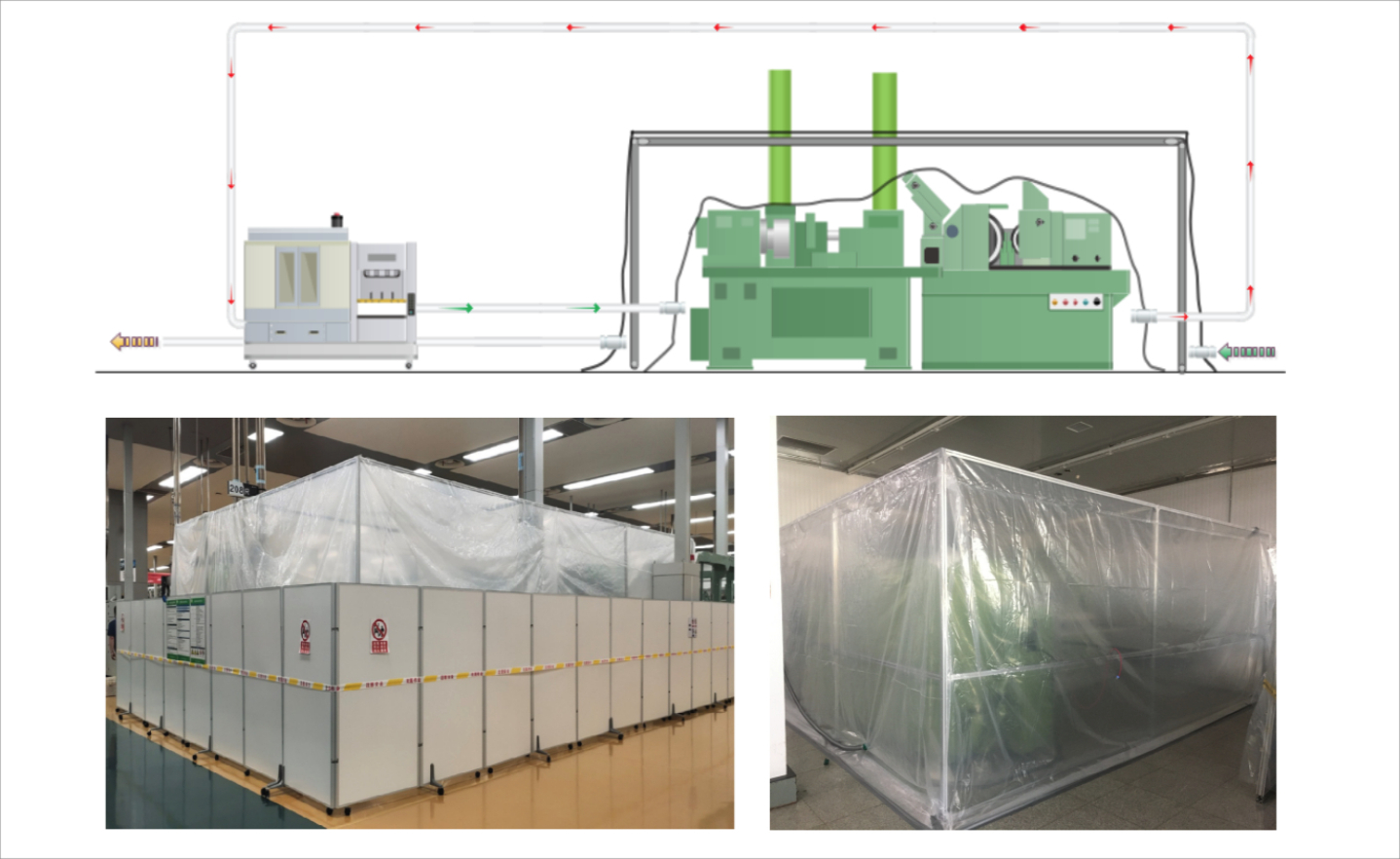
- 遇虫情突然爆发需短期内降低虫害风险时,可采取应急化学治理。
- 应急处置前,结合虫情会诊与虫源排查,灵活安排区域全面或深度物理清洁。
- 应急处置后,完成环境通风、机台表面清洁、药剂残留监测,之后方可入场。
- 锚定虫源隐患进行持续的精准治理,巩固防治效果。
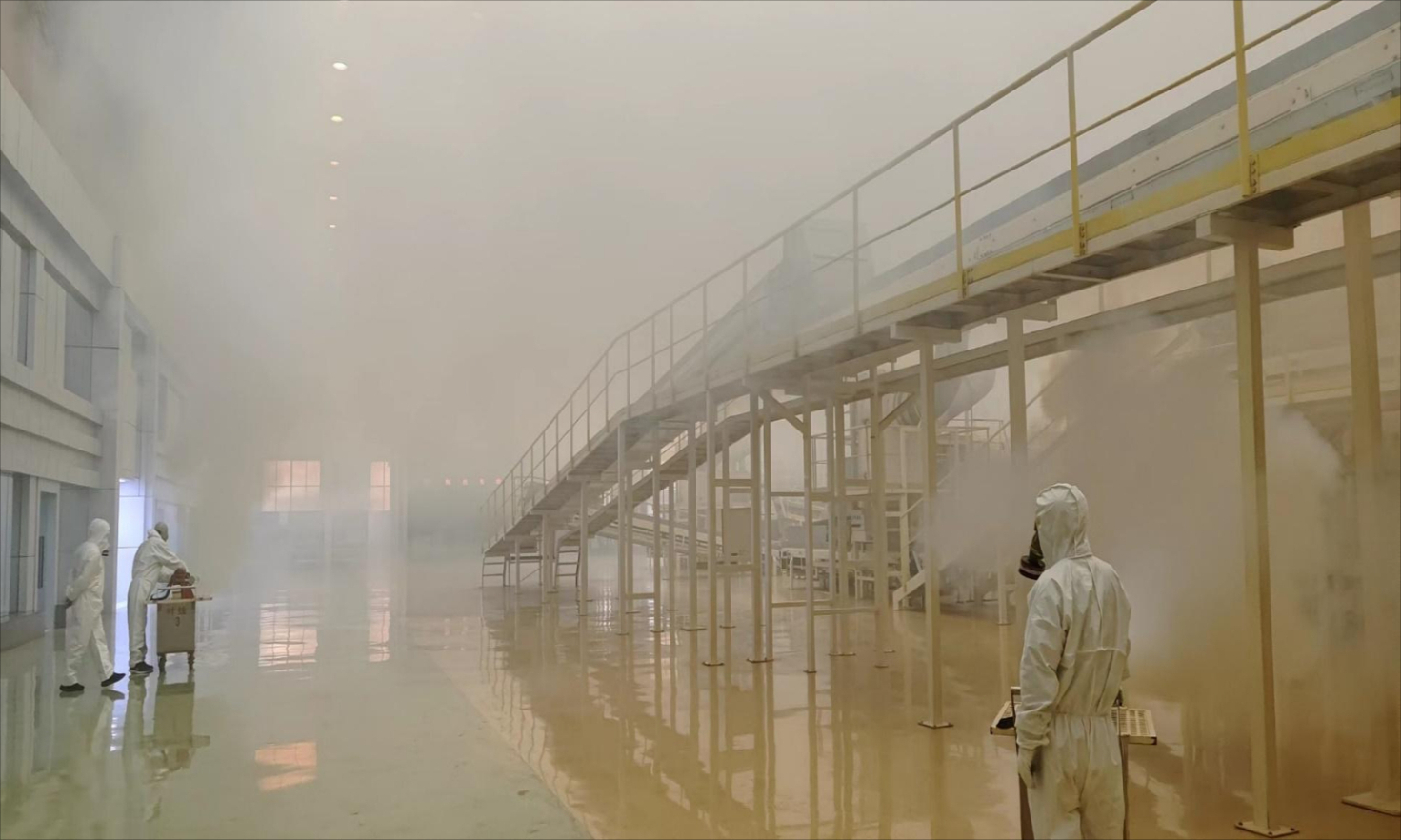